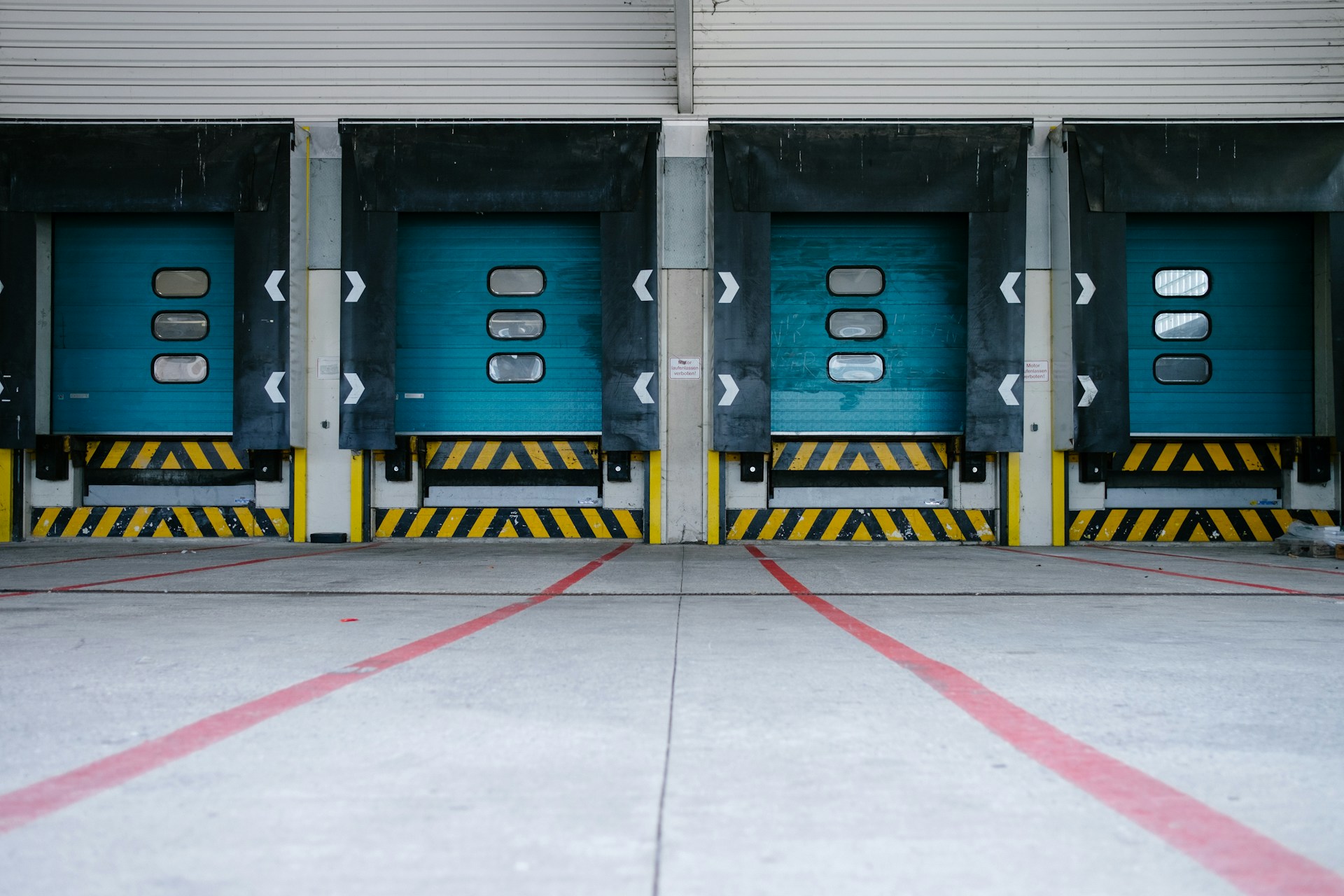
How Cross Docking Streamlines Your Supply Chain?
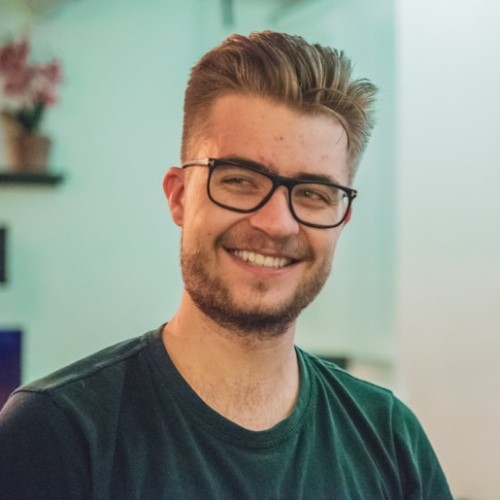
Cross-docking is a valuable logistics method that helps businesses deliver products faster while increasing the efficiency of supply chains. By directly moving goods from inbound to outbound shipments, companies can minimize or eliminate the need for warehouse storage and reduce handling costs.
When products arrive at a facility, they are immediately prepared for shipment to retail locations or customers rather than going into storage. This streamlined process skips the steps of unloading, shelving, picking, and loading inventory. Cross docking reduces the time products spend waiting in warehouses from days or weeks to just hours or minutes.
Faster Delivery Times
The seamless transfer between inbound and outbound trucks at our shipping hub enables expedited delivery times for all packages. As soon as inventory arrives from suppliers, it is sorted and loaded directly onto outbound trucks heading to customer locations across the region. Without the need to unload and reload shipments, orders spend less time sitting idle and more time traveling to their final destinations.
Our streamlined shipping process significantly reduces the total time required for an order to reach the customer. The direct transfer of goods between trucks eliminates unnecessary delays and keeps each shipment continuously moving through our system. Customers receive their purchases sooner and enjoy the convenience of faster delivery.
In today's world where immediate access is expected, speedy and dependable shipping is a crucial competitive advantage. Our efficient operations model sets a high standard for prompt order fulfillment and rapid product delivery. Customers can always rely on us to get their goods where they need to go as quickly as possible.
Lower Operating Costs
By implementing just-in-time inventory management, businesses can greatly reduce the amount of warehouse space and staffing required. Just-in-time inventory management aims to have materials arrive exactly when they are needed in the production process, thereby minimizing inventory on hand. This avoids the costs associated with storing excess product.
With less physical inventory to manage, businesses can get by with smaller warehouses that require fewer employees to operate. The reduction in overhead and labor expenses goes straight to the bottom line. Just-in-time inventory management streamlines operations while simultaneously cutting costs.
Improved Inventory Management
Tight inventory control is crucial for businesses with limited storage capacity. To avoid tying up capital in excess inventory, companies aim to carry no more stock than absolutely necessary. This lean approach requires keeping a close eye on inventory levels and turnover rates.
One technique that supports minimal inventory is cross docking. With cross docking, products are received at a warehouse and prepared for immediate shipment to customers, without ever going into long-term storage. The goal is to speed products straight through from suppliers to end users in a just-in-time fashion. This reduces the need for maintaining safety stock and frees up precious warehouse space for active inventory.
By constantly monitoring stock levels and moving inventory swiftly to customers, businesses can operate in a lean and efficient manner. With diligent oversight of inventory management, companies can maximize their return on capital while minimizing unnecessary storage costs. Adopting cross-docking procedures and just-in-time practices allows businesses to optimize inventory turnover in tight quarters. With a lean, nimble approach, companies can keep stock lean yet still meet customer demand.
Increased Flexibility
The flexibility of distribution centers is greatly enhanced through cross docking. This streamlined process allows products to move through the facility rapidly, without the need for storage. As shipments arrive, they can be quickly sorted, consolidated if needed, and loaded onto outbound trucks. The minimal handling and storage time enables distribution centers to adapt nimbly to fluctuations in supply and demand.
Cross docking provides the agility to handle a wider variety of products seamlessly. In a traditional warehouse, available storage space constrains the range of inventory that can be accepted. With cross docking, products simply flow through the facility, removing these limitations. Distribution centers can take on new product lines and adjust volumes in real time based on changing requirements. This versatility is invaluable in today's dynamic business environment.
The ability to pivot quickly provides competitive advantages in responsiveness and efficiency. Cross docking shrinks lead times, allowing businesses to meet spikes in customer demand rapidly. Minimal storage also reduces costs associated with inventory handling and occupancy. As market conditions shift, cross docking gives distribution centers the flexibility to cost-effectively adapt their operations. This agility is key for companies looking to thrive in volatile markets.
Better Visibility
Customers demand faster fulfillment, and competitors race to meet those expectations. This situation calls for supply chain visibility - the ability to track shipments in real time across your network. Direct transfers between facilities grant that visibility and reveal data to optimize your operations.
Direct transfers involve moving goods directly from one site to the next, bypassing distribution centers. RFID sensors, GPS tracking, and other technologies follow shipments step-by-step through transit. The data streams into your logistics platform, providing total visibility from start to finish. You gain instant insight into shipment locations, conditions, delays, and more.
With that real-time tracking, you can spot and resolve bottlenecks as they occur. Issues like production lags, transport snags, and inventory shortfalls become transparent. You can take instant action to keep the supply chain flowing smoothly. Data-driven decisions might involve adjusting production schedules, re-routing shipments, or re-stocking inventory.
Conclusion
In today's fast-paced business environment, companies must be nimble and efficient to stay competitive. An effective strategy to enhance logistics agility and speed up order fulfillment is cross docking. Cross docking is a practice in logistics and supply chain management where items are unloaded from an incoming semi-trailer truck or railcar and directly loaded into outbound trucks, trailers, or containers, with little or no storage in between.
The optimized material flows that cross docking facilitates are critical advantages in today's customer-focused business climate. By leveraging cross docking, companies can deliver orders faster and more efficiently. This allows them to better serve customers, foster loyal relationships, and gain an edge over the competition. As the pace of business continues to accelerate, cross docking will become an even more vital strategy for companies to embrace.